Project Management and Industrial Engineering
Potentials in the Product Development Process (PDP) – you have to ask the right questions at an early stage.
We find that our customers have a high level of experience and expertise in the development of their products. When designing processes, specifying and industrializing production systems, the right questions are often not asked from the outset to get things right.
There are many reasons for this. Among other things, it is due to communication, corporate culture, roles and responsibilities, interaction between the departments involved, change management and a lack of process understanding in the value chain.
We review your organization and your processes, work with you to identify your potential and help you implement sustainable measures.
If you would like to find out more, please contact us.
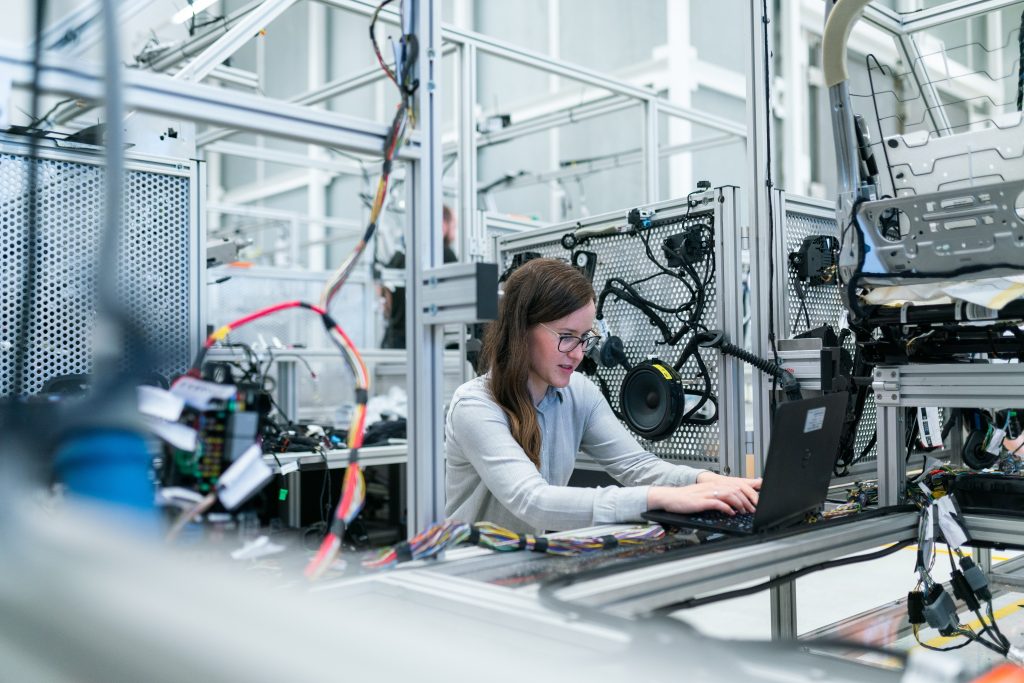
Relevant project topics
Would you like to find out more? Contact us – we are at your disposal!
Potential analysis
Identification of optimization opportunities along the value chain.
Project organization and communication
Structuring projects, effective reporting and establishing a clear organizational structure
Prozessablauf, Materialfluss- und Layoutplanung
Process flow, material flow and layout planning
Planning and approval of industrialization concepts
Development and implementation of sustainable production concepts.
Start-up capability of new processes
Ensuring the operational readiness of new processes and systems.
Production start-up
Monitoring and controlling the start of production to ensure quality and efficiency.
Training and coaching
Training courses such as IE Lean training and preparation for customer visits.
Interim management
Bridging management vacancies with practice-oriented expertise.
Selected projects
- Project Management
- Business Case
- IE-Lean Training
Based on a quick check in project management, collaboration between product development (Product Center), local project management and manufacturing engineering was optimized. This led to shorter lead times, clear responsibilities, more efficient reporting and reduced start-up and capex costs. Quick-win solutions were implemented and prioritized measures were implemented step by step.
A business case for the partial plant expansion with relocations, new investments in production facilities and an optimized logistics concept was successfully created. This involved defining relevant premises, validating existing analyses and developing various scenarios with detailed cost and savings analyses. The decision paper provides a sound basis for the economic evaluation of the plant expansion and the associated potential for cost reduction.
A lean training course for technical planners (industrial engineering) was successfully developed and implemented. The training is based on company-specific requirements and an established standard process for planning approval (e.g. lean certificate). This strengthened the understanding of lean principles, improved planning quality and increased efficiency in the approval process.
We are specialists in the introduction and further development of excellence and quality systems, the optimization of plants, plant and production processes and effective escalation management.
Laforet Consulting GmbH | Copyright © 2025
Homepage designed by Laforet-IT