Production and Logistics
Waste-free production and logistics processes are clear competitive advantages – consistent action is often lacking
Many magic words are used to give the impression that the value chain is well under control. Companies have introduced production systems, have a shopfloor management system, have coordination rounds to excess – some are surprised that the approach doesn’t really work. It doesn’t take long for the whole system to “fall asleep” – after all, it hasn’t achieved anything.
There are many reasons for this – the driver of the initiative leaves the company or even cost pressure. Savings are being made in the wrong places.
In our view, inconsistent action is a major barrier to operational excellence.
Take a look at the key figures that you track on the shopfloor every day. What do they tell you? Are they even the right metrics? What about the measures? Too many open issues that are not completed? Too many repeat failures because you don’t get to the bottom of the real causes? What happens? The consequences are often missing.
We help you to set up an excellence system, use it correctly and develop it further so that you have a robust and adaptable value chain.
Relevant project topics:
- Potential analysis, value stream mapping
- Establishment and further development of production systems
- Establishment and expansion of production capacities
- Adaptation of production structures, work organizations and logistics processes
- Optimization of production planning and control
- Increasing the efficiency of indirect processes (e.g. Sales and Operations Planning, TPM, MRO)
- Sustainable cost reduction in direct and indirect areas
- Preparation and realization of relocations
- Training & coaching (e.g. working with key figures, value stream mapping, lean methods)
- Interim
If you would like to find out more, please contact us.
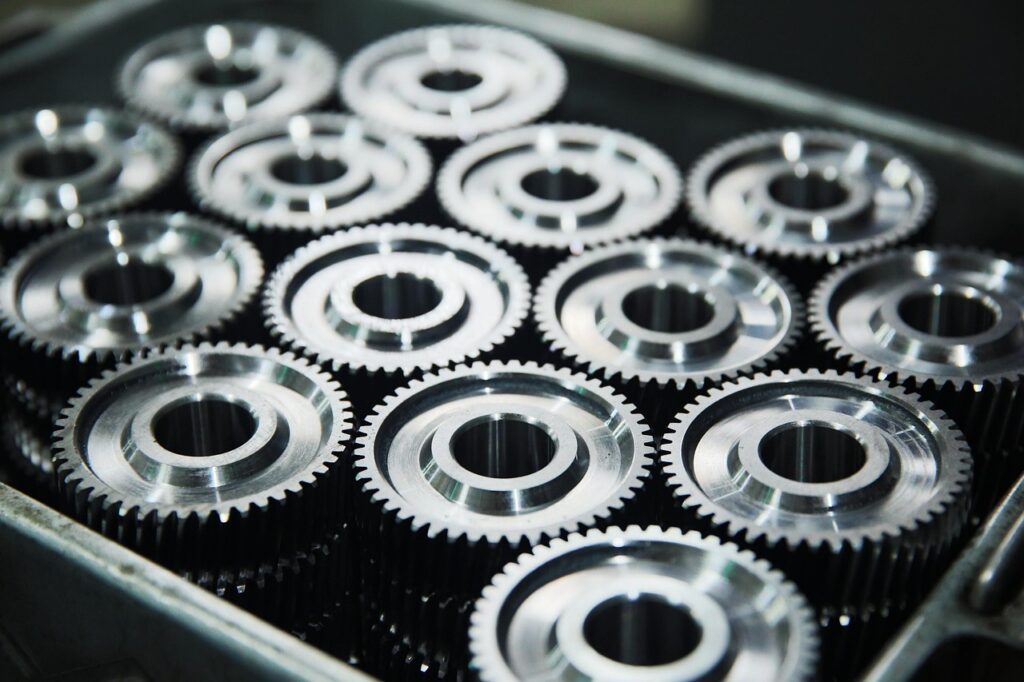
Relevant project topics
Would you like to find out more? Contact us – we are at your disposal!
Potential analysis, value stream mapping
Identification of opportunities for improvement along the entire value chain.
Establishment and further development of production systems
Introduction and optimization of robust systems to increase efficiency.
Establishment and expansion of production capacities
Planning and implementing sustainable capacities to ensure growth.
Adaptation of production structures, work organizations and logistics processes
Efficient design of production processes, work organization and material flows.
Optimization of production planning and control
Improving planning security and resource utilization.
Increasing the efficiency of indirect processes
Optimization of areas such as Sales and Operations Planning (S&OP), Total Productive Maintenance (TPM) or Maintenance, Repair and Operations (MRO).
Sustainable cost reduction
Implementation of measures to reduce costs in direct and indirect areas.
Preparation and realization of relocations
Structured planning and implementation of location changes without compromising quality.
Training & coaching
Training in topics such as KPI management, value stream mapping and lean methods.
Interim
Taking on management tasks in transitional phases or in the event of special challenges.
Selected projects
- Project Management
- Business Case
- IE-Lean Training
Based on a quick check in project management, collaboration between product development (Product Center), local project management and manufacturing engineering was optimized. This led to shorter lead times, clear responsibilities, more efficient reporting and reduced start-up and capex costs. Quick-win solutions were implemented and prioritized measures were implemented step by step.
A business case for the partial plant expansion with relocations, new investments in production facilities and an optimized logistics concept was successfully created. This involved defining relevant premises, validating existing analyses and developing various scenarios with detailed cost and savings analyses. The decision paper provides a sound basis for the economic evaluation of the plant expansion and the associated potential for cost reduction.
A lean training course for technical planners (industrial engineering) was successfully developed and implemented. The training is based on company-specific requirements and an established standard process for planning approval (e.g. lean certificate). This strengthened the understanding of lean principles, improved planning quality and increased efficiency in the approval process.
We are specialists in the introduction and further development of excellence and quality systems, the optimization of plants, plant and production processes and effective escalation management.
Laforet Consulting GmbH | Copyright © 2025
Homepage designed by Laforet-IT